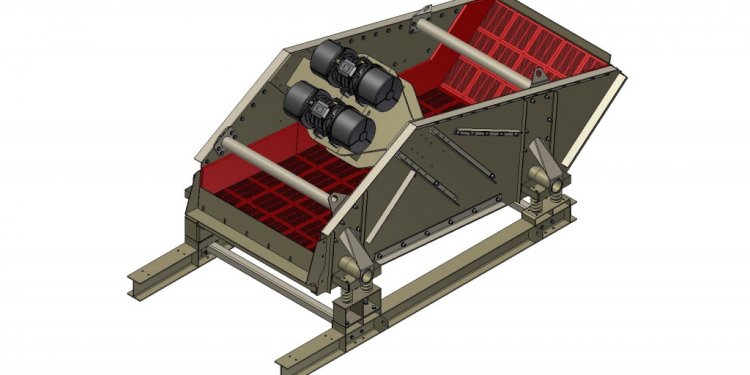
Astec Asphalt
Warm Mix Systems for Continuous Mix and Batch Plants
The benefits of warm mix asphalt such as reduced energy consumption, lowered emissions, and elimination of visible smoke are well-known in the asphalt paving industry. Warm mix technology allows mix to be prepared and placed at lower temperatures, typically 50°F to 100°F lower than conventional hot mix. To achieve this, the viscosity of the asphalt cement (AC) must remain low at the reduced temperatures. Maintaining a low viscosity at lower temperatures allows mix to flow freely through storage, transfer and placement equipment and is more easily worked by hand.
Unfortunately, many technologies for warm mix production rely on additives, special asphalt cement, special procedures and/or special AC delivery systems to achieve low viscosities at low temperatures. The additives are expensive and add significant cost per ton of mix. Astec warm mix systems eliminate the need for expensive additives and special asphalt cement by mixing a small amount of water into the AC to create microscopic bubbles. These small bubbles act to reduce the viscosity of the AC coating on the rock allowing the mix to be handled and worked at lower temperatures.
Water is delivered to the system using a positive displacement piston pump capable of accurately metering water into the system. Using feedback controls, pump speed is modulated to maintain the appropriate flow of water based upon the flow of AC. PLC controls provide for smooth and consistent water flow as production rates increase or decrease.
Water is injected into the liquid AC through a series of all stainless steel injectors located above corresponding foaming chambers. AC flows through the foaming chambers where water and AC are thoroughly mixed to produce mechanically foamed AC.
A skid-mounted corrosion-free water reservoir is provided with an automatic filling valve. If supply water is lost, a low-water alarm alerts plant personnel so the problem may be resolved quickly without wasting mix.