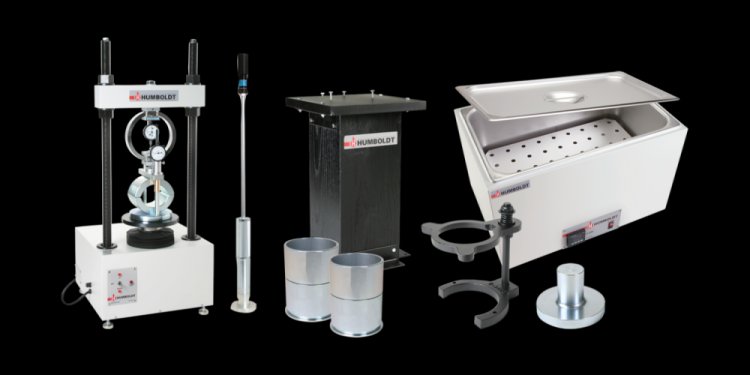
Equipment for road construction
•
Comprehensive methodology was developed to model the emissions of on-road construction equipment.
Three types of instruments, including a PEMS, a GPS-INS and an engine data logger, were used to collect field data.
Engine load was identified as a crucial parameter in modelling emissions based on operational parameters.
Quantitative model was developed to estimate emissions of on-road construction equipment at operational level.
The model developed in the paper estimated emissions of on-road construction equipment with more than 89% accuracy.
The construction industry is considered to be one of the largest contributors to greenhouse gas (GHG) emissions globally. Emissions from construction equipment are normally estimated through simulation or conducting emission tests in the laboratory, which may not represent real-world situations. Field data measurement is essential to quantify the emissions of equipment in use. This paper aims to develop an operational level model to estimate the emission rates of carbon monoxide (CO), carbon dioxide (CO2), hydrocarbon (HC) and nitrogen oxides (NOx) of on-road construction equipment. The data collection procedure included instrumentation, laboratory testing and field measurements. Three types of instruments, including a portable emission measurement system (PEMS), a global positioning system-aided inertial navigation system (GPS-INS) and an engine data logger, were used to collect emissions rates, operational parameters and engine data, respectively. The raw data collected from the three channels were then synchronized and validated. Further, the operational level emission model was developed by performing ordinary least square (OLS) and multivariable linear regression (MLR) analyses of the field data. The emission model considers engine specifications, operational factors and environmental parameters as affecting variables. The statistical analysis results verify the high correlation between emission rates and affecting parameters. The developed model is finally validated by comparing the estimated results with the real data collected by the PEMS and the engine data logger in the field experiments.