June 26, 2018
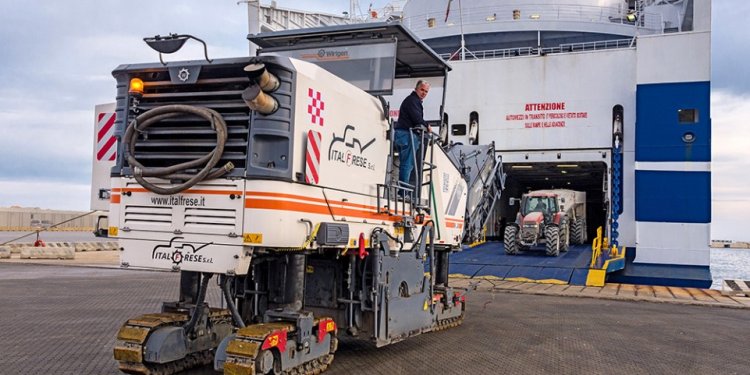
Used Wirtgen milling machines
of adhesive material called tack coat. It is generally agreed by different researchers (Canestrari et al. 2005; Hachiya & Sato 1997; Mohammad et al. 2002; Raab & Partl 2009; Miro et al. 2005; Uzan et al. 1978) that the application of tack coat in pavement interfaces yielded a better bond, yet it is still sadly to say that there are still contractors and consultants trying to ignore the effect of tack coat in pavement construction. The reason remains unknown since tack coat can be considered a relatively cheap material compare to the overall pavement construction cost. Tack coat can be in the form of asphalt emulsion, paving grade asphalt and cutback asphalt. Of the three materials, asphalt emulsion proved to be the most popular tack coat material, not only in Malaysia but also being applied globally (James 2006). Although the application of tack coat is beneficial, however, there are still several other factors dealing with tack coat application which can further affect the bonding in the design stage. Such factors include tack coat types, tack coat application rates, temperature and mix type. Besides, there are also construction factors during the construction stage which can weaken the bond development. This paper will discuss on the constructions factors in enhancing the bond development. The main objective was to share the information pertaining to previous studies in pavement interlayer bond strength conducted by researchers worldwide, hoping that the local asphalt industries can benefits from these information and mark an increment in the quality of finished work. Other factors affecting the pavement interlayers bond strength had been presented elsewhere (Yaacob et al. 2013). In Malaysia, dense graded asphaltic concrete ( AC ) is still favored despite the introduction of mixes like stone mastic asphalt and porous asphalt. It is generally assumed that the constructed dense graded AC is dense enough such that water from the surface runoff has no chance to penetrate into the surfacing course. Yet, problems related to poor bonding still occur at an alarming rate and caused serious losses, to both government and the tax payers. This gives an indication that construction quality might be the dominant factor over the problem related to poor bonding. In fact, problems related to poor bonding in pavement surfacing course are no longer new issues. These problems include slippage failure, being the most typical. Huang (2004) and Smith (1979) describe slippage failure as crack in a crescent shaped crack where the two ends usually point in the direction of the traffic. This failure usually occurs when there exist insufficient bond between the interfaces of the two layers in contact. Such statement is further agreed by Chen (2010) and West et al. (2005). At location where vehicle is likely to exert high horizontal force, sharp curves and busy junction of continuous acceleration and deceleration, slippage failures may be frequently encountered as well (Romanoschi & Metcalf 2001). Besides, delamination of surface layer also seems to be a distress related to poor pavement interlayer bonding (Santucci 2009). Several real cases incorporating the problems related to poor bonding have been reported by researchers worldwide (Charmot et al. 2005; Chen 2010; Pavement Interactive 2008). Computer analysis conducted by King and May (2003) and Roffe and Chaignon (2002) after West et al. (2005) also agreed that pavement service life is significantly reduced when the bonding is insufficient. Due to that, maintenance work usually approached earlier. Delamination and potholes can be considered as one of the most common types of pavement distress related to poor bonding in Malaysia, though slippage failure can be occasionally found. Figure 1 depicts some of the pavement distresses encountered in Malaysia due to insufficient pavement bond. Design mix, tack coat types and tack coat application rates are among the design factors which can affect the quality of bond developed in an interface for a layering mechanism. As discussed in previous section, construction factors and practices can have significant effect as well, especially when to apply the designed criteria into practice in a proper manner. A good quality of work ensures the effectiveness of tack coat and at the same time enhanced the performance of the constructed pavement. It is therefore can be concluded that layer bond strength is a complex function of both design and construction factors. In order to achieve optimum bond strength, each factor needs to be carefully monitored and investigated. The subsequent section will discuss some construction factors which are most likely to prevent the proper development of bonding strength between pavement surfacing layers. These factors include curing time of asphalt emulsion tack coat, surface condition and technology, workmanship and quality of construction. Asphalt emulsion is a mixture of bitumen, water and emulsifying agent under a pre-determined proportion. It is suggested that rapid setting type of emulsion like RS -0k and RS -1k is to be used as tack coat materials ( MS 161 1994). Proper application of asphalt emulsion as tack coat in construction is important. In the presence of water, asphalt emulsion need to be properly cured in order to ensure the degree of tackiness prior to paving work. Often, the term ‘break’ and ‘set’ is encountered when dealing with the asphalt emulsion as tack coat materials. According to OHIO (2001), the term, ‘break’ is used to describe the initiation of the process whereby water, introduced during emulsification, separates from the asphalt cement and begins to evaporate. As for ‘set’, it occurs when the water within the emulsion has completely evaporated, leaving a layer of thin asphalt cement on the pavement with adhesive properties. The importance of curing asphalt emulsion has been verified by many researchers. As early as 1998, survey result by Paul and Scherocman (1998) over Department of Transportation of various states in The United States found that paving work is generally began only after the emulsion is completely set. Some states like Alaska specified maximum curing time of 2 h for cationic slow set ( CSS -1) emulsion, Arkansas allowed up to 72 h for slow set ( SS -1) and Texas specified maximum curing time of 45 min for SS -1 or medium set ( MS -2). Buchanan and Woods (2004) also suggested that longer period of curing time will increase the bond strength. Laboratory test using cationic rapid set ( CRS ) emulsion and styrene–butadiene–styrene ( SBS ) modified asphalt emulsion ( MAE ) from Chen and Huang (2010) also indicates that curing time of 30 min can help to increase the development of bond strength although it is not very significant. Later, it is reported that curing time significantly affected bond strength developed as higher bond strength seems to be a resultant of longer curing time (Tran et al. 2012). At the same time, there are also publications and guidelines on application of asphalt emulsion tack coat need to be properly cured before any operation that followed by shall commence (Blades & Kearney 2004; Cross & Shrestha 2005; Mohammad et al. 2012; WSDoT 2003). Although it is frequently being mentioned that curing time is important, the exact time for which the emulsion to be cured is unclear and varies from location to location. The curing time largely depends on the weather condition and the types of emulsion used in the particular area. For best result, laboratory testing on the curing time should be carried out to determine the curing time before the application of tack coat emulsion on site. At the same time, there exists no consensus over the necessity of laying HMA layer under cured asphaltic emulsion tack coat. Real cases where paving over unbroken tack coat yet resulted in satisfactory bonding strength is reported. West et al. (2005) conducted field project using the Novachip TM construction process which enabled asphaltic emulsion tack coat to be applied just before the laying of HMA loose mix to evaluate the bond strength between pavement layers. They concluded that the bond strength measured is significantly higher. Testing by Tashman et al. (2008) discovered that curing of tack coat to increase interface bond strength is insignificant regardless of the test methods, either by adopting FDOT shear tester or torque bond test. Due to the inconsistency in test result among the previous researches, Pavement Interactive (2011) concluded that influence of curing time over bond strength is not well corroborated. Construction practices in Malaysia do apply tack coat to provide sufficient degree of adhesion between pavement layers ( JKR 2008). In resurfacing or a new road construction project, while waiting for trucks of asphaltic concrete material to be delivered, the asphalt emulsion tack coat is applied throughout the section of road to be paved and will have sufficient time to break and set. But, this might also raise concern as tack placed too far ahead of the paver might lose its tack characteristics and should be retack according to Construction of Hot Mix Asphalt Pavements, Manual Series No. 22 ( MS -22). This can be explained as tack coat exposed will be polluted by the dust particle from construction as well as vehicles passed by. Accumulated dust will then prevent a proper bond development as the surface area in contact is reduced due to the presence of dust particle. As for maintenance work, especially in patching work, tack coat is also applied. However, due to time constraint and pressure from heavy traffic flow, asphalt emulsion applied is generally insufficiently cured which then resulted in poor quality of work. Often, the similar distress over the patched area recurs after certain period of time opened for trafficking. Such nature of work should be avoided at once and to be replaced by proper steps of maintenance to minimize losses, both in financial and manpower aspect. Today, curing of asphalt emulsion to enhance layer interface bond strength may still be questioned by different parties. Despite that, it is strongly suggested and recommended for the Malaysian road construction industry to properly cure the asphalt emulsion tack coat before any paving work shall begin. As pavement layer interface study is still at the beginning stage in the country, curing of asphalt emulsion should be favored until a more comprehensive study is achieved, like the development of Swiss Standard SN 671 961 in the Switzerland and Austrian method which provide the minimum shearing force to be fulfilled for constructed pavement. Only after that further research on the necessity of tack coat emulsion curing can be examined by referring to the guideline. At the same time, curing time of asphalt emulsion needs to be maximized although in real cases it might be rather difficult to deal with. It should also be understood that curing of asphalt emulsion is interrelated to climatic conditions like wind speed and certain inherent material properties (Banerjee et al. 2010). Exposure to sunlight from tropical country like Malaysia should be fully utilized to ensure that asphalt emulsion is fully cured. This will help to prevent flushing and slip plane for paving over unbroken and uncured tack coat emulsion (WSDoT 2003). Surface condition is another factor which can greatly affect the interface bond strength between layers of flexible pavement. Roughness or texture, cleanliness and wetness are among the common surface condition which is most likely to be encountered on site. Roughness or texture may be associated with the milling operation whilst cleanliness and wetness is a result of dust and weather condition. In order to enhance the bond strength, surface condition at the interface need to be taken extra care of, both before and after the application of tack coat. Milling practice is rather common in Malaysia over a resurfacing work, especially to road section with severe surface distress. Milling tends to correct problems like rutting, shoving, bleeding and at the same time maintained the headroom and guardrail height for safety purposes. In some previous research, it is also reported that milling operation, which often result in the existence of certain degree of roughness on the pavement will help to increase the bonding strength between the layers (Al-Qadi et al. 2008; Cooley, 1999; Mohammad et al. 2010; Sholar et al. 2003; Tashman et al. 2008). In some research, it is even reported that application of tack coat over a milled pavement contributes no adhesive properties to the interface, which indicates that the friction among the layers in contact has become the dominant factor in providing the shear strength upon loaded with vehicles load (Cooley 1999; Sholar et al. 2003; Tashman et al. 2008). Due to that, it is always recommended that milling is done prior to paving work in order to generate sufficient friction to counter the shear forces exerted from the traffic. A resurfacing work in Johor Bahru area involved a dual lane road with approximately 1.5 km length. As usual, the road section is milled, by using Wirtgen milling machine W1900 as shown in Figure 2. Milling depth is about 50 mm. As milling involved removing of pavement surfacing materials, it is unavoidable to leave behind on the pavement with dust and loose material after the process which is certainly harmful to proper bond development (Jeevan 2007; McGhee & Clark 2009; OHIO 2003). This has become the major concern for milled pavement and for that, the contractor used a power broom to clean the milled section thoroughly, minimizing the effect of dust from milling as shown in Figure 3. Meanwhile, for unmill pavement, pavement surface cleaning is also needed to remove organic or inorganic matters which is encountered during construction. This agrees to Caltrans (2009) and Hansen (2008) which suggested that tack coat should be applied on dry and clean surfaces which is cleaned by means like power broom, vacuum sweep or high pressure flush, depending on the surface condition for which cleaning method is to be applied. Santucci (2009) has an interesting finding where thoroughly cleaned roadway surface upon tack coating not only increase bonding ability but at the same time capable to minimize pick up on tires of construction equipment. This is certainly an important finding in road construction but it is not clearly discussed in the publication over the minimizing of tires pick up in relating with the clean pavement surface. Despite plenty of publications and guidelines which emphasized on the importance of clean pavement surface, there existed also research results which indicate that dirt do not actually inhibits the bond development between the layers (Cooley 1999; Hachiya & Sato 1997; Patel 2010). Besides dust, existence of moist on pavement could be another factor which hinders the bond development between pavement layers. Moist can be in the form of rain, especially for tropical country like Malaysia where sudden change of weather is unexpected or water left behind from the milling process. For water left behind after milling process, the effect will be less significant during sunny day, but in a cloudy weather, it might just be that the pavement is at a surface dry state instead of completely dry. The relatively high humidity and low evaporation rate will lengthen the construction, which is hardly managed to follow by the contractors. Application of tack coat at this time in wet and dust condition will serve no purpose. This agrees to research result by Raab and Partl (2009) who investigate the influence of cleanliness and moisture on pavement surface before the application of tack coat material. In the presence of moist and dust which is a normal phenomenon at the construction site, the shear strength tested using layer parallel direct shear ( LPDS ) tester when compared with the control sample marked a significant lower shear strength. Similar setup and testing is applied to reinvestigate the influence of cleanliness and moisture existence after the application of tack coat. This even worsens the bond strength where many of the cores have actually lost their bond even during the coring process. Sholar et al. (2003) did similar testing by applying water over cured tack coat simulate the rainy condition encountered during construction. The end result is a great reduction of shear strength observed in the presence of moist. Research by Patel (2010) contradicts the finding by concluding that moisture has no severe effect over the bond development for the range of tack materials tested which includes trackless, SS -1h and SS -1, except PG 64-22 that fail to create any bond in wet conditions. This inconsistency of information proved that bonding between pavements layers may varies and is of extreme sensitive with regards to the test configuration setup and the parameters involved. In another words, by simply altering just a parameter, a different trend of testing result might be observed. Under such circumstances, it is rather impossible to question the reliability of these information as the research conducted are tested with different test configuration with different shear testing device. As Malaysia is still working hard to excel further in the research of pavement bonding development, those previous research will certainly provide useful information to generate appropriate guidelines to be applied locally, taking into considerations of local factor like environmental and weather condition. Technology revolved and enhanced from time to time, offering ample new features with better qualities. Continuous research carried out worldwide resulted in new technologies, especially in road construction equipment, road materials, green and sustainable construction as well as laboratory devices. It is generally agreed that highway engineering technology in Malaysia remain lagged behind compared to the Western countries, or even Asia countries like Japan and China. Although local asphalt industry might have been exposed to the latest technologies from overseas through various workshops and conferences conducted by well-known academicians and researchers, but in terms of implementation, there is still a big gap apart. A typical example is the method of application of tack coat. The Western used an asphalt distributor truck as early as 1980’s to apply tack coat or prime coat. Figure 4 shows the application of tack coat using an asphalt distributor truck. One major advantage of using the asphalt distributor truck is to provide a more uniformly distributed tack coat on a surface to be paved, which ensure the curing rate of asphalt emulsion for the entire pavement to be constant besides having a faster operation time and capable to adjust the target spread rate of tack coat. As in Malaysia, the typical method of applying tack coat is still by using hand wand sprayer as shown in Figure 5, which is generally time consuming and normally ended up with non-uniform spread of tack coat. Tack coat distributor truck does exist, but its use is only limited to large scale project. Application of tack coat by both methods certainly resulted in different spraying quality, in which asphalt distributor truck will definitely provide a better spraying quality. This is simply due to the fact that the asphalt distributor truck consider a variety of significant factors which may affect the spraying of tack coat like spray bar height, nozzle angle of the spray bar, sufficient pressure to force the tack coat through the spray bar and the truck speed itself while spraying the tack coat. All these factors are well discussed with attached figures by OHIO (2003) and Caltrans (2009). Another concern for tack coat application using hand wand sprayer is the consistency of the tack coat application rate as specified by JKR (2008). If such method of tack coat application remains, the specification will serve no purpose since it is rather impossible to accurately calibrate the desired application rate using the hand wand sprayer (West et al. 2005). Even worst, non-uniform application will certainly be a norm to this method, resulted in formation of ponding of tack coat at a certain location as shown in Figure 6, thus affecting the curing rate of asphalt emulsion and provide the slipping plane between the layers due to excessive application. Such construction quality may explain the frequency of delamination distresses to occur so rapidly in the country. Quality construction involved quality control (Satterfield 2005). Quality control is a process to measure and ensure the quality of an end product is achieved. This process involves consistent inspection and evaluation throughout the project construction period. Without proper supervision, poor quality construction workmanship is to be expected as outlined by Ahmad (2002) after Chong (2006). A site supervisor should be very familiar and experienced with the project so that the information provided to the labor on site is accurate and the construction is according to the standards and specifications. Besides supervision, the importance of project monitoring and materials quality to achieve quality construction is also mentioned by Ahmad (2002). As early as 1993, Low (1993) had emphasized the importance of practicing the skills possessed in order to produce quality of workmanship desired. Apart from that, the importance of ISO certification in affecting the workmanship quality has also been verified (Iwaro & Mwasha 2012). According to the Immigration Department of Malaysia, the total number of foreign labors recorded in Malaysia up to August 2011 exceeds 2.3 million people, which can be considered as a large number of populations. With this large amount of population, sufficient supervision by site supervisor during construction becomes inevitable. Despite usually unskilled, the major drawback with foreign labor is communication as most of them only spoke their native language. Coincidentally, poor workmanship as a result of poor communication is also supported by previous research (Thomas et al. 1998). Ineffective communication resulted in an unsuccessful information sharing. Due to that, the foreign labors will normally imitate the others in order to get the job done. They have difficulties neither to understand the theory behind a particular action nor to discover any possible faulty element which they encountered during construction as in Figure 7. They simply not able to cope with details like premix temperature, compaction temperature, emulsion application rate, whether it is a residual application rate or not and factors discussed earlier like curing and surface condition prior to paving. In fact, they should be properly trained before involving in the real construction work, but it is indeed sad to say that such opportunities are often overlooked and never provided by the contractors. C ONCLUSION The quality of bond between pavement layers must be carefully monitored during construction. Technology shortcomings in Malaysia might prevent the implementation of better construction practice but there should always be an effort to introduce new technologies into the industry in order to increase the competency of the country. At the same time, having to get to know all possible construction factors, the construction industries should make full use of this information to increase the quality of the construction. Curing of asphalt emulsion should remain and the cleanliness of pavement surface should also be ensured by minimizing the existence of dust particle. These could be done if proper supervision is done on site by a qualified personnel when the work is carried out. While the Western countries have progressing much further in the related research, developing country like Malaysia should also follow the path to produce similar research pertaining to pavement distresses due to insufficient bonding, taking into consideration of the local factors, especially the weather of being a tropical country.