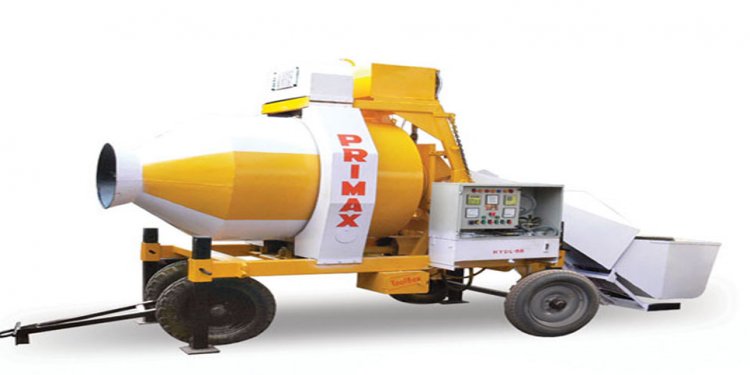
Civil construction equipment
Enstruc were approached to support a new project mobilisation plan for the design and construction of a number of strategic roads and junctions worth over $100m. The request was to supply a combination of new and used construction plant, machinery and trucks including; concrete batching plants, asphalt batching plants, motor graders, hydraulic excavators, bulldozers, compactors, asphalt pavers, tipper and service trucks. Other critical supplies included 30 tonnes of high quality timber and phenolic film faced plywood for concrete formwork and workshop use, pneumatic tubular forms for the construction of underground main drainage, various survey and test equipment, geosynthetic ground preparation materials, advanced drainage solutions, dewatering pumps, generator units, tools, road safety signs, street furniture, site safety and personal protective equipment.
OUR APPROACH
- To support our customer in providing a mobilisation budget, Enstruc produced a procurement budget containing full product specifications, quality standards, lead times, logistics information and costs for all required construction plant, equipment, trucks and supplies; sourced from over 20 leading manufacturers, across 6 different countries.
- The procurement budget was approved by the customer and Enstruc commenced phase 1 of the proposal by carrying out a full inspection on all capital purchases and returning the reports to the customer for final approval. Any used goods that required maintenance works to meet customer requirements were carried out prior to delivery.
- FSC timber and plywood samples for concrete formwork use were sent to the customer for evaluation and approval.
- All goods were placed on order by Enstruc during phase 2, with a staggered delivery schedule to meet our customer's build schedule.
- Regular supplier visits and expedite meetings were conducted to provide a secure supply chain and alignment with delivery schedules and agreed quality standards.
- Any anomalies and quality concerns were controlled and managed by Enstruc in a timely manner to ensure there were no delays to the contract schedule.
- All goods were checked, consolidated, intelligently labelled and securely loaded for onward delivery, according to the customer delivery schedule. Multimodal transport was used, as well as a mixture of one-way shipping containers, roll-on/roll-off and break-bulk shipping were utilised to deliver. Smaller more urgent items were air freighted.
- 12 months service and maintenance packagaes for plant and equipment were provided within the supply contract. All one-way shipping containers were purchased for the customer to provide safe site storage.