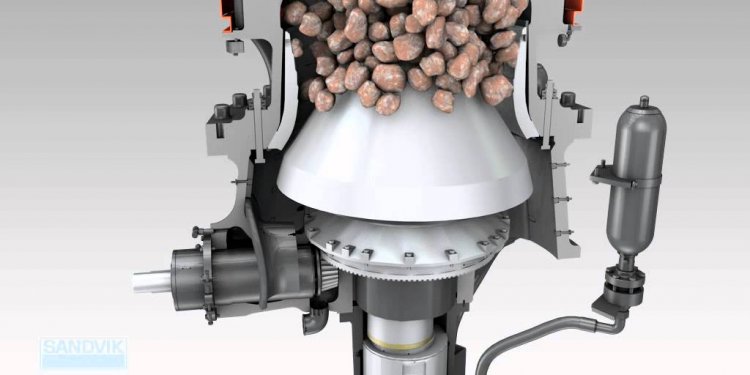
Impact Crusher VS cone Crusher
When it comes to crushing for use in concrete and asphalt, most experts agree that cubical stone is ideal.
Most crushed stone and sand is produced for use in concrete and asphalt, and there is general agreement that a cubical stone is ideal for use in these products. “The more elongated and flaky the material is, the more water, cement or binder you require, ” says George Fensome, area manager, Americas, for Sandvik Construction’s crusher product line. “A cubical aggregate allows you to reduce the amount of cement and water, while still producing a strong concrete product, so it is better. The benefit is similar for asphalt, ” he adds.
According to Bradly Estes, plants manager, Western Region, for Granite Construction Co., natural sand is cubical in nature. When it comes to crushing aggregate to form a cubical particle, the geologic makeup, crushing stage and type of crusher all play a part in producing the desired end product, he says.
For instance, in a sedimentary deposit such as limestone, the strength of some rock is lower in one direction than in another due to mineral cleavage and other weak layers that occur in the parallel planes. Rocks with these characteristics tend to become flat and elongated when crushed — especially with compression crushing. “Impact crushing, more specifically with rock-on-rock action, helps such stone to break along its natural lines, rounding off weak edges and sharp angles so that the particle more closely resembles natural sand, ” notes Estes.
The goal with primary crushing is to reduce the particle size. Some refining of shape may take place in the secondary stage, but most particle refinement for shape takes place in the tertiary and even the quaternary stages. “Many operators will try to crush with only two stages, but you usually need at least three stages, ” Fensome says, explaining that feed size plays into this. A primary jaw or impact crusher may take a feed with a top size of 39 inch. The secondary crusher could take an 8-inch to 10-inch feed. The top size feed for the tertiary crusher may be 4 inch, but typically it is 2 inch.
“If you have a jaw, and you’re going for a 2:1 or 3:1 ratio, a 36-inch rock suddenly goes to a minimum of 12 inch, ” Fensome continues. “That means you’re feeding a 12-inch rock at the secondary stage to a crusher that may accept a top size of only 8 inch because you’re trying to reduce it too quickly.
“People often try to save a penny at the start of the process, and it ends up costing them a dollar more in the end. You can’t cut corners, ” he adds.
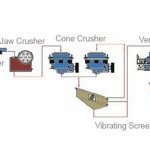
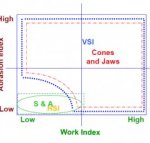
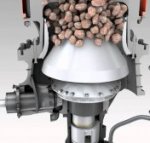
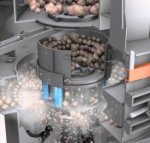