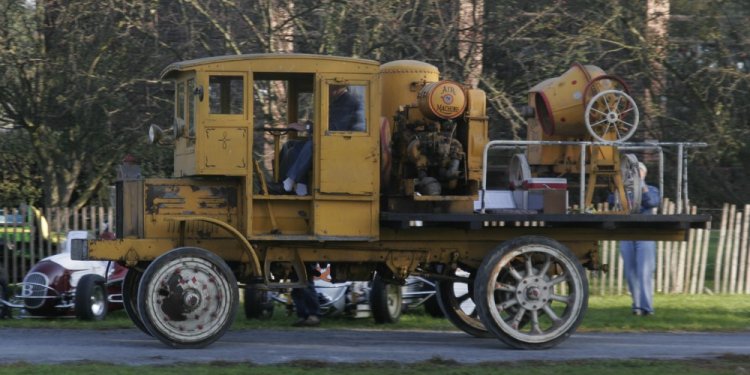
Antique Concrete Mixer
Utilizing this website, check out our “Distributor Locator” section, just click on the desired distributor and get linked up with one of our fantastic teammates.
Prism Pigments is proud of the thousands of colors we formulate. Our standard mortar case covers 111 colors and our standard concrete color card includes 42 colors. However, our ability to match colors or blend special colors is almost endless.
Prism Pigments are designed to be dosed as a % of cementations, which must include fly ash or slag products. Most of our loadings range from 1% to 5%.
Prism Pigments are produced from only the finest grade of pure synthetic iron oxides and do not fade.
Prism Pigments Five For Twenty
Prism Pigments Concrete Colors are pure, synthetic iron oxide pigments containing no fillers that will affect the performance of the concrete mix design. Prism Pigments concrete color applications provide the user with a lightfast, weather resistant, lime-proof, no maintenance finished product. Prism Pigments maintain the highest tinting strength and color consistency from bag to bag. Prism Pigments Concrete Colors are ideal for use for integrally colored concrete in highly visible areas such as driveways, patios, walkways, car paths, curbings, athletic courts, or stamped concrete. A stable, weather resistant color is always the end result.
Composition and Materials
Prism Pigments Concrete Colors contain only finely milled synthetic iron oxides, the strongest and most stable colors available. These colors are lime-proof, sunfast, inert, and meet or exceed the criteria of ASTM C979. Colors
Prism Pigments Concrete Colors cover the full color spectrum: brown, buff, tan, black, yellow, orange, red, green, blue, and white. Each color match is handled on an individual basis. In cases where exact color matching is required, samples of your field raw materials may be required for sample preparation. Concentration Rates
Prism Pigments Concrete Colors are available specially packaged for your on-site use. Because of the inherent tinting strength of synthetic iron oxides, standard loadings do not exceed 8%. Levels greater than 8% will not enhance the finished color. Mixing Precautions
Always follow approved mixing practices, which include the following tips:
a) Cement for the entire job/project should be from the same manufacturer. Changes in cement will effect the final cured color.
b) All aggregate, fine or coarse, should be supplied from one source and be non-reactive.
c) The mix design must be consistent from batch to batch. If the batch size is changed, the pigment must be also.
d) Concrete slump should not exceed 5″.
e) Clean the drum before and after mixing.
f) Add color directly into the mixer with the other ingredients. Mix 5-10 minutes. Placement of Concrete Slab Work
A successful slab starts with a well drained subgrade that can sustain the load imposed on the slab. The subgrade should be graded, compacted, dampened. Prevent soft spots, standing water. Minimize handling. movement and spreading of colored concrete for the color consistency. Do not overtrowel, as this will cause darkening. Do not finish until bleed water has left the surface to protect against scaling, efflorescence and uneven coloring. Placement of Vertical Concrete
Planning is crucial in placement of vertical and poured-in-place concrete. Consider types of cement, detailing of formwork, mixing and placing techniques, slump control, and temperature of cure. It is recommended that a field mock-up panel be prepared. Include all materials, reinforcing steel as in the finished project. Design Criteria for Colored Concrete
The following points should be considered in designing colored concrete. The concrete temperature should be between 65 and 85 degrees. Timing of the arrival of concrete trucks is crucial so that there is no excessive mixing. Avoid using porous forming materials. Conveying methods must be consistent with ACT-304-13. The concrete should be deposited in level lifts 12-18″ thick. The distance between insertions should be generally about 18″ depending on the concrete mix and vibrator used. Tilt-up concrete panels should be textured using sandblasting and surface retarders to expose the course aggregate. Patching Colored Concrete